What and how is grass made? This post gives you some knowledge and a thorough understanding of artificial grass manufacturing. We’ll get started by making artificial grass yarn.
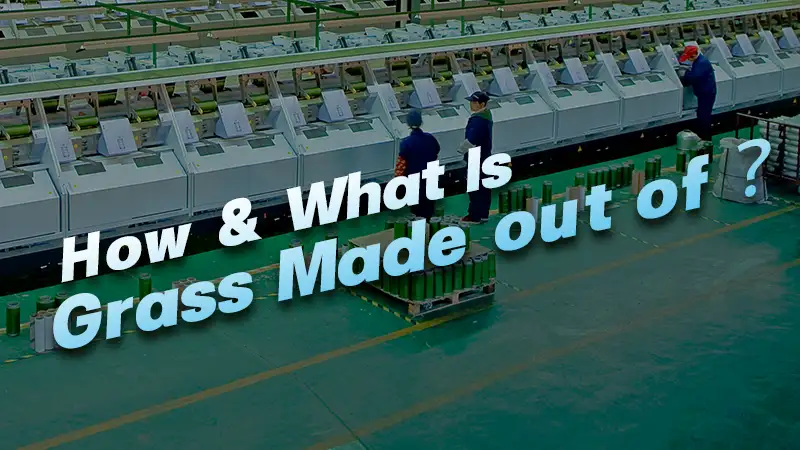
Yarn Production Process of Artificial Grass Manufacturing
Extrusion is the technique used to create the fiber used in fake grass. Simply put, raw polymer pellets are combined with coloring and UV additives before being converted into tape or individual fibers. These are then twisted and wound onto spools, delivered to the following step in manufacturing fake grass.
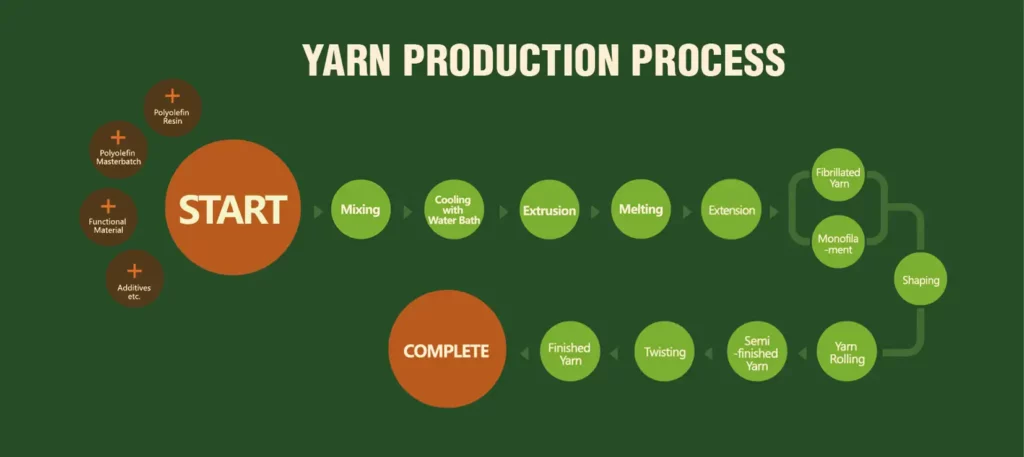
Material
What materials makeup grass? Initially, nylon (PA), then polypropylene (PP), and now primarily polyethylene (PE) were used to create artificial grass.
The most popular polymer grade is C4, while more sophisticated artificial grass producers utilize C8, which is cleaner and more durable. Although more expensive, this aids in creating yarns that last longer.
Fibrillated or monofilament
After melting and mixing the identical raw ingredients, two distinct but related production processes are carried out. A perforation pattern is applied to the fibrillated yarn to make a tape that can be tufted to give it the look of grass. The monofilament yarn is the main topic below.
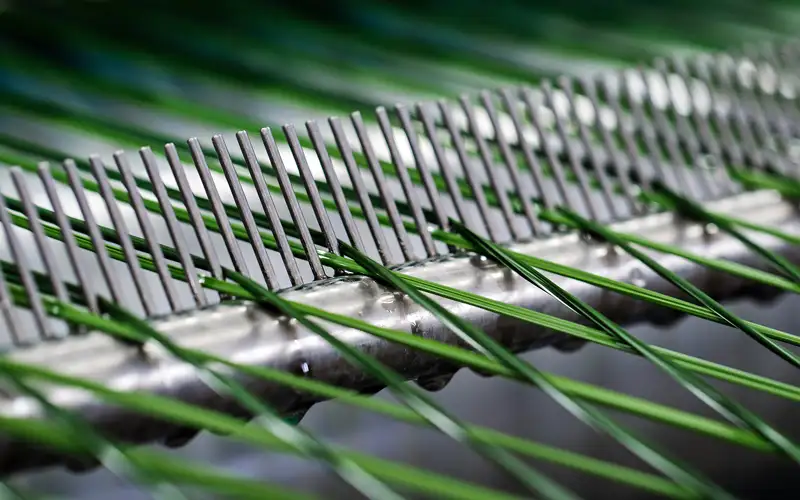
Shape
Different forms can be made with monofilament yarn. This enables design flexibility, with some shapes—like diamonds—proving more durable and robust than flatter strands. The strongest product on the market is our flagship item, Superb, which employs cutting-edge C8 grass yarn and has a diamond-shaped design.
Like toothpaste, the hot, still-pliable mixture is forced through a specially-made dye and onto individual fibers. These are then chilled and stretched before joining groups, eventually forming the tufts in the finished lawn.
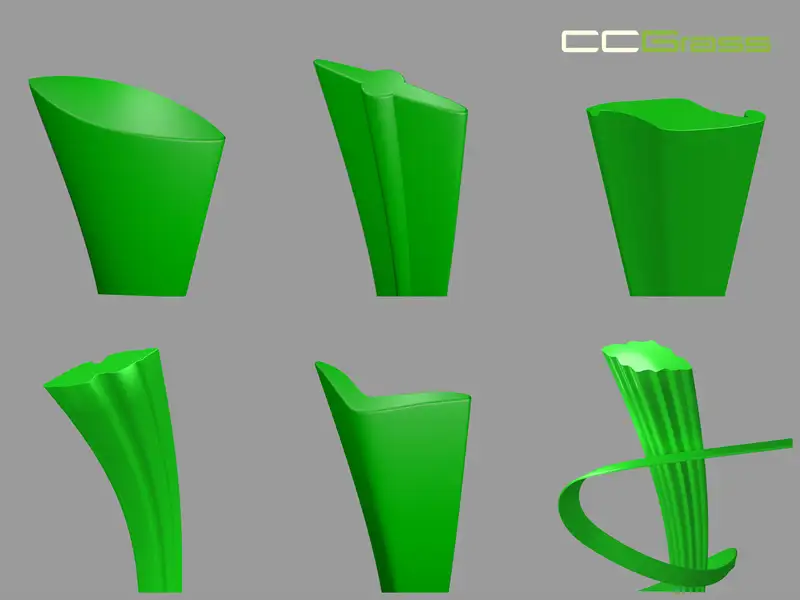
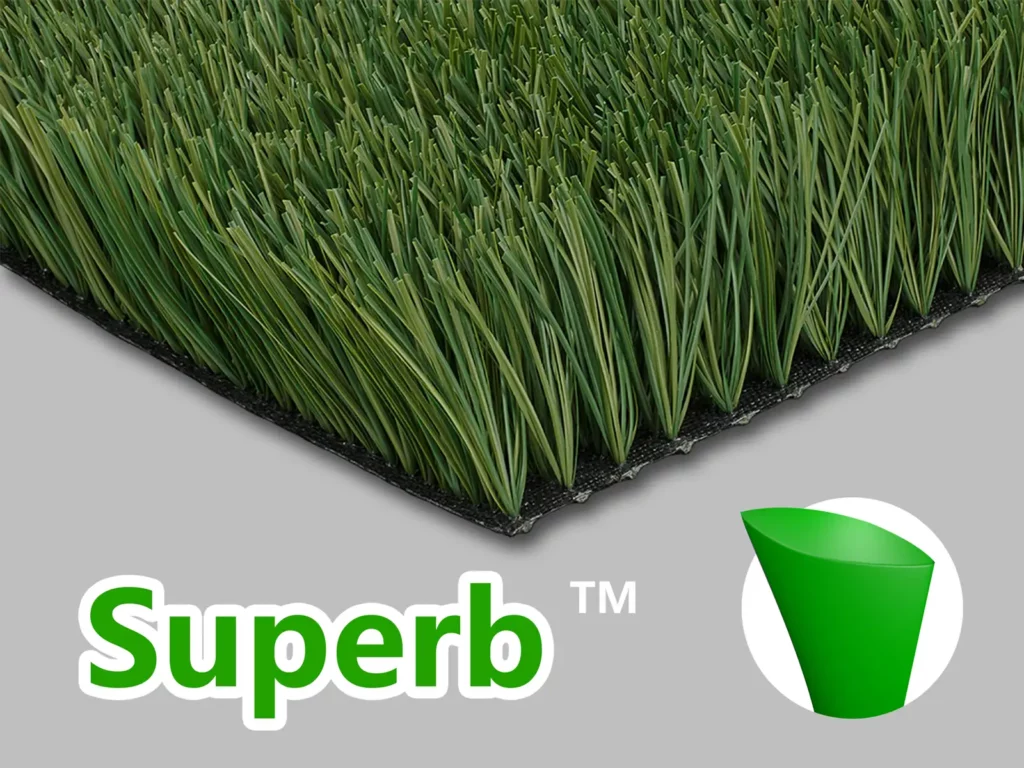
Color
The master color batch is introduced right as the extrusion process starts. At this stage, variously colored yarns can be produced. A master batch often yields a certain amount of color, sufficient to fill numerous fields. However, a perfect match is not always achieved when comparing one specific green master batch to another of the same color.
Emerald, olive, lime, and forest are the most popular colors of green that can be combined to create a more natural-looking grass appearance in a single tuft.
We have many shades of grass for sports like hockey, padel, and tennis to enhance the contrast of the ball in various settings. They come in several colors, including traditional green, diamond blue, and others.
Weight
The different yarn shapes produced determine the yarn weight or Dtex. The Dtex will typically be 12,000 but may go as high as 17,000 for sports. The greater weight would indicate that the individual fibers would be wider and thicker, which might be too enormous for the tufting stage of production.
Yarn weight uniformity is crucial for the finished product to match test results and product standards.
Texturized yarn
During extrusion, a curl is introduced to yarn made for hockey. A lighter yarn, typically around 8,000 Dtex, is utilized, twisted, and heated to set the twist in place.
The yarn must be texturized on a different machine in a second stage, or the curl can be applied “inline” using an “inline” method, which is less frequent. Both methods result in uniform curls, the size of which can be adjusted as the process progresses. “In the line” is quicker and more economical.
In house production
With their extrusion equipment, in-house manufacturers of fake grass have much more freedom to create unique yarns, control costs more effectively, and have total command over their supply. Costs can be kept down by holding a small amount of stock yarn in “just in time” manufacture, which is also an option.
Warranty
Most monofilaments come with a warranty of at least five years. Depending on usage, those constructed of C8 polymer give a longer guarantee period of up to 12 years.
Turf Production Process – Tufting of Artificial Grass Manufacturing
The method used to make fake grass is that fiber is tufted into a background fabric and then cut into individual tufts.
Equipment
Equipment Turf can now be manufactured more quickly, accurately, and efficiently thanks to an updated, computerized, and faster tufting machine.
A creel behind each tufter contains the yarn spools created during extrusion. The design and loading procedures employed in a creel help to increase production effectiveness.
The backing cloth roll holder is located just behind the tufter. By doing this, one backing sheet is fed into the tufting machine. To help with eventual tuft lock and carpet stability, many businesses will have two feeders that allow different backing fabrics to be blended.
The needles to which the yarn is threaded and the sharpness of the knives that cut the fiber to the right length are two components of the tufting apparatus where accuracy and quality are crucial.
Various tufting machines are employed to create turf with a long or short pile. The gauge, or the separation between each needle, controls this. A 3/16-inch gauge would be utilized for hockey, whereas a 3/4 or 5/8-inch gauge would be used for football grass with a longer pile.
The tufting machine operates more quickly, the broader the gauge. The machines are also programmed to generate a variety of pile heights, with the lowest pile heights starting at 9mm and going as high as 70mm on the wider gauge tufting machines.
Before the tufted grass is moved onto stage 3 of the process, the backing line, the repair and check area, is the last component of the tufting setup.
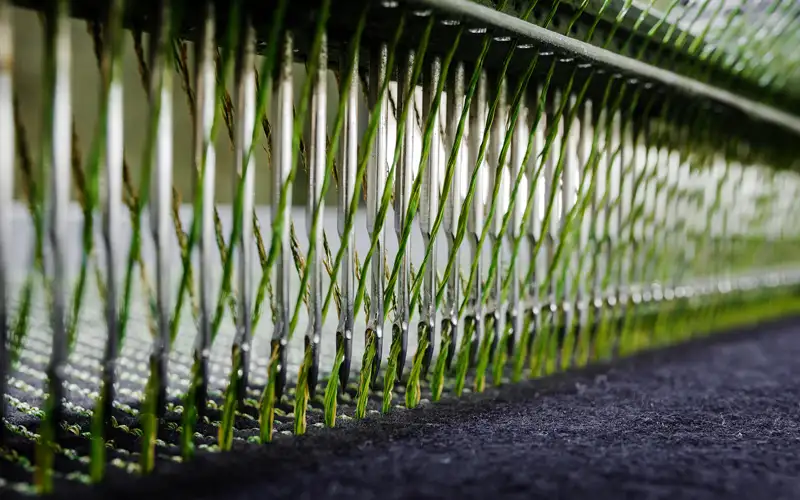
Operators
While some expertise is involved in this procedure, quality turf is produced more by paying attention to the little things. The creepers and tufting team must have the proper mindset and training.
A creeler, tufting operator, and checker would make up a typical tufting team during the finishing stage of the operation. Additionally, it is anticipated that Quality Control, who would be in charge of a set of tufting machines, would frequently inspect each stage.
Process
The yarn is fed into the needles by being drawn from the creel and through tubes. To ensure accuracy and verification, these are numbered. The backing material is progressively pushed into the tufting area as the needles pierce the yarn. Knives cut the loop at the proper length to form the tufts, and the roll continues at the correct speed to establish the proper number of tufts per linear meter.
The machine stops, and the yarn is mended if a yarn breaks. Once the repair is finished through the back of the lawn in the checking area, the front is trimmed to fit the necessary length.
The tufted turf is prepared for delivery to the backing area when fed through.
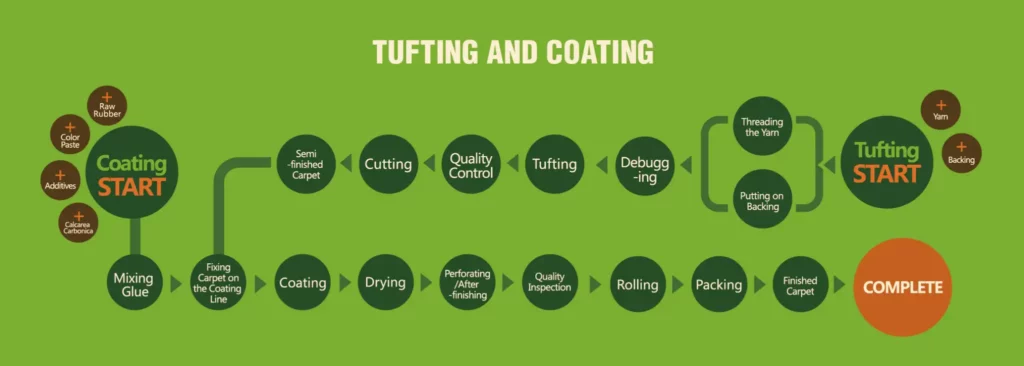
Turf Production Process – Backing of Artificial Grass Manufacturing
This procedure completes artificial grass production by ensuring that the fibers are fastened to produce the finished synthetic lawn.
Types of secondary backing
The basic backing fabric or cloths, which only loosely hold the synthetic grass fibers in place, have already been tufted with the synthetic grass fibers. Transporting the tufted rolls to the backing line makes them ready for the following step in the process. Latex or polyurethane (PU) are the two types of supplementary backing currently used.
Equipment
A modern backing line is made up of various parts, each of which is essential to the production of artificial grass. Most backup lines are at least 30 meters long, and some are longer. The size of the ovens used to dry the turf’s back determines this. These ovens have temperature controls because if the temperature is off, the backing may not dry properly or overcook.
Any backup line must have a location where final quality checks can be performed.
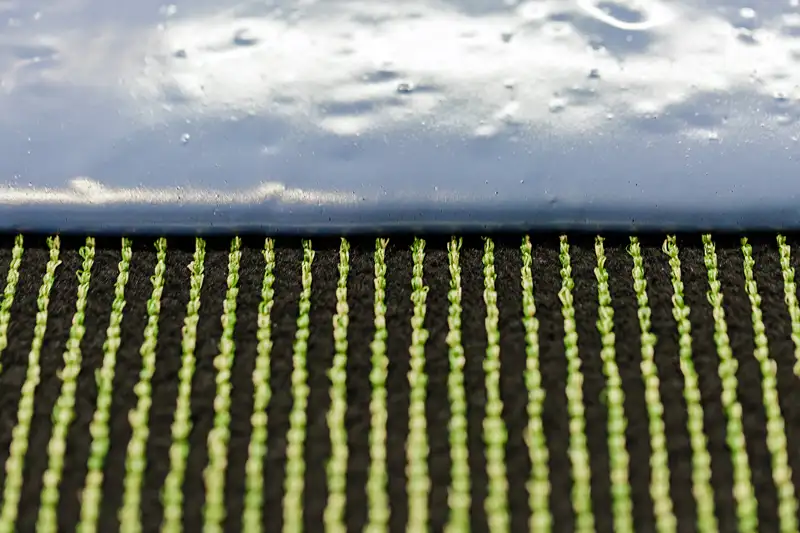
Method
The unbacked grass is first pushed fiber-down onto a flat surface, covering the primary backing with secondary backing material. The same outcome can be accomplished in various methods, resulting in complete coverage of the tufted turf’s back.
The secondary backing is then dried by pulling the turf through a succession of ovens where heat is delivered to the back. The turf’s fiber side is exposed to controlled heat, allowing the individual fibers to expand.
Drainage
As the grass, which has been backed, exits the ovens, it moves through a region where drainage holes have been drilled into the turf, spaced equally apart to ensure future, quick drainage. The turf is then suspended into collection bins and prepared for last-minute examination.
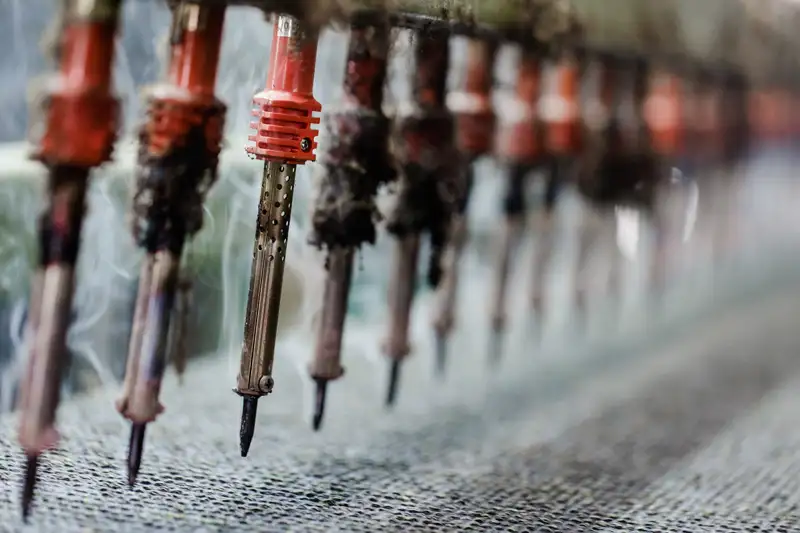
Final checks
There are quality checks performed at several stages. These include monitoring the temperature of the ovens, confirming the backing has dried, and ensuring drainage holes are properly applied, as well as evaluating the consistency, application, and weight of the utilized latex or PU material. Final checks, which include visual inspection and particular product testing, are crucial to the finished product’s quality.
Before each roll is rolled up and packaged for transportation, it passes through an inspection area where it is watched. Here, the fiber length, stitch density, and other quality control metrics, along with the tuft lock’s strength, are checked. These are kept on file in case there is a problem later.
Although the examination area is as well-lit as feasible, detecting lawn problems in artificial light is only sometimes possible. On occasion, spot checks involve unrolling an entire roll outdoors in the open air while examining for product uniformity, color variations, and line straightness.
The artificial grass production side is finished once the turf’s quality is validated. Discover how CCGrass, the top turf producer in the world, creates fake grass in this video.
The significance of the roll-up unit, delivery preparations, and final dispatch will be discussed next.
After Production – Wrapping, Packing, Shipping, and Unloading
The excellent synthetic turf must reach its destination in pristine shape.
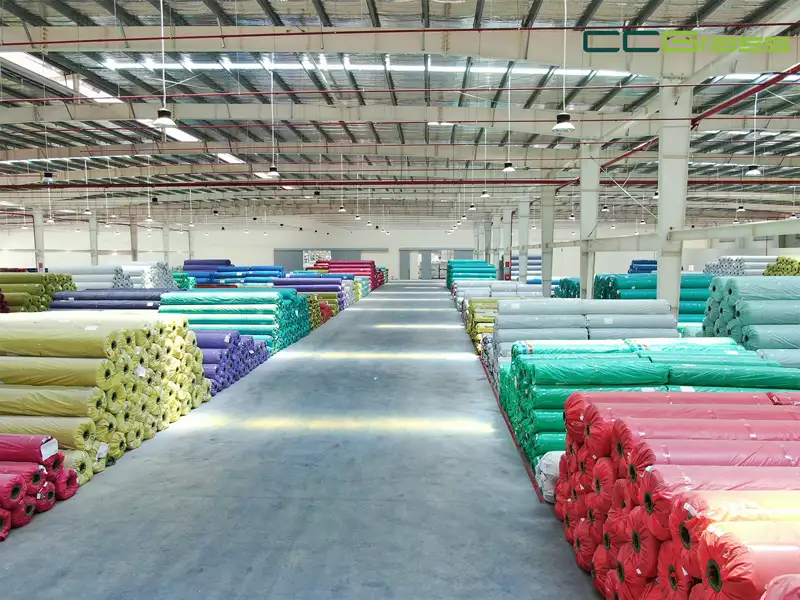
Wrapping
When backed and examined, turf is securely rolled and prepared for transport. This might seem straightforward, but if done incorrectly, it could result in several issues at the job site. These can include turf that develops wrinkles or rolls that become loose after shipping and are difficult to unroll. Before being cut to the necessary length, the roll-up machine pulls the turf tightly as it is passed through to avoid problems.
To stop water from leaking a while on-site, the rolls are wrapped in a plastic covering and fastened at either end. Each roll has a number corresponding to a spot on the layout diagram.
Packing
Rolls are loaded into the shipping container’s floor or on top of one another using long booms on large forklift trucks. Smaller rolls (less weight) can fit more in a stack than larger rolls (which can be piled three high). Strong cardboard lines the container’s floor and sides to avoid damage.
Ideal roll transportation involves only one handling of the roll from manufacturing to the site. The designated shipping agent will handle delivery to the destination port, where a local shipping agent will arrange for the synthetic grass buyer to pay customs and port fees before delivering to the site.
Unloading
A forklift with a long boom is required to remove the rolls from the container. The role is hoisted out of the container after the boom has been put through the center tube to the far end. Rolls back in the container are moved forward until the boom can remove them completely.
The inner tube may break due to improper equipment (short boom) or ineffective unloading practices (boom not inserted far enough). The turf may then “pinch” as a result, developing minute creases. The identifying document for each roll should be checked to ensure it is still connected. This aids in ensuring that rolls are unrolled into the proper position.
Before the grass is unrolled, each roll should be inspected for any visible damage (torn wrapping), which should then be reported.
A premier artificial grass manufacturer, CCGrass, is committed to offering the best turf for landscape and sporting applications. Please visit the official CCGrass website for more information on artificial grass. Call +91 99586 77005 or email info@gallantsports.rightsymbol.us if you have any additional inquiries concerning the manufacture of artificial grass.